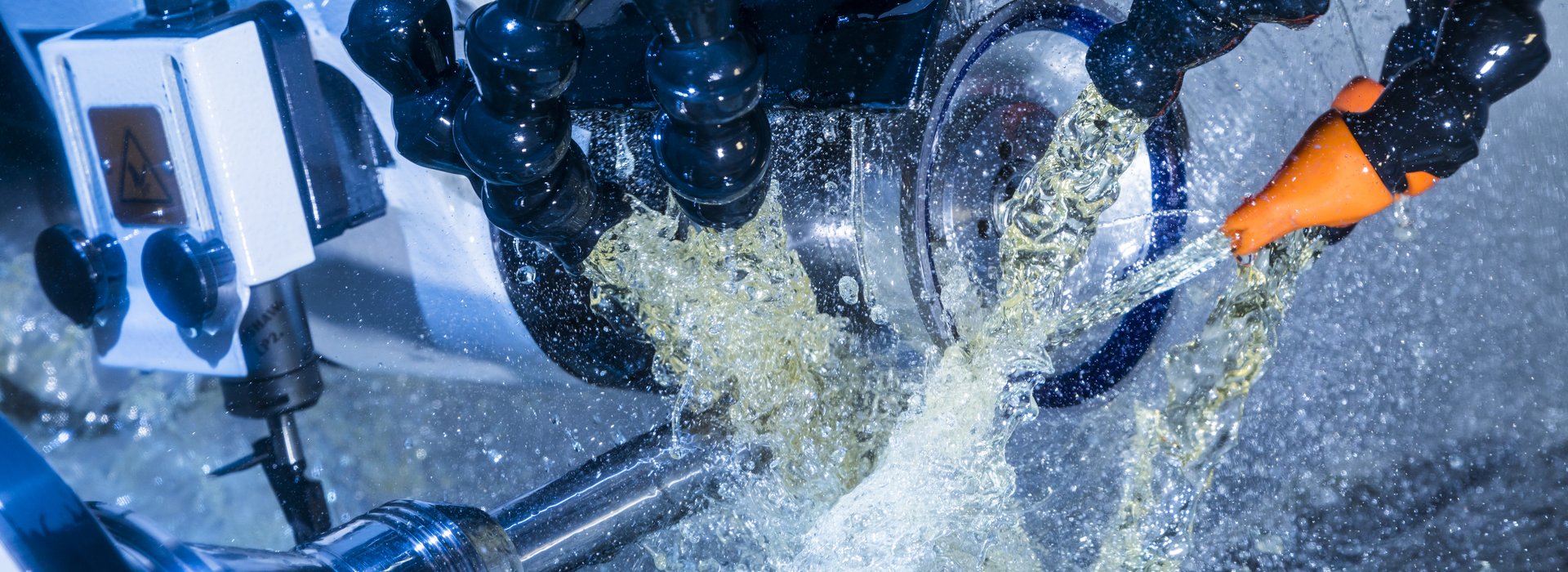
Regrinding of solid carbide drilling tools at the highest level:
In tool management projects, TCM is not only responsible for the procurement, provision and ongoing optimization of the cutting tools, but also for professional reconditioning.
In some of the current TCM tool managements, we have a high proportion of shank tools, which often make up more than 70% of the entire tool portfolio
As is well known, the tool costs per part (CPU) can essentially be influenced by 3 factors:
• Increase in service life (Technology Team)
• Reduction of the purchase price (Purchasing Team)
• Increase in the number of regrindings (Technology Team + Grinding team)
Especially with solid carbide drills and step drills, a low CPU can only be achieved through frequent regrinding with professional quality.
The prerequisites for this are state-of-the-art grinding and measuring equipment, a well-thought-out process, and the ability to precisely restore the tip geometries of the drilling tools that have been ground by the manufacturers.
The difficulties that often arise here are:
• Large variety of tip geometries from the different manufacturers
• Thermal influence on the cutting material after first use
• Deterioration of the surfaces on the bevels on the outside diameter
• Removal of the PVD coating on the bevels and in the flute
• Broken cutting edges, complete breaks
• Falling short of the specified minimum lengths
Condition of the round bevels after repeated use with delamination:
Over the years, TCM has been able to gain a lot of experience in its own grinding operations and thereby continuously improve internal processes.
In this way, a consistent reprocessing quality, the basic requirement for a constant long service life, can be permanently guaranteed.
When a drilling tool is reground by TCM for the first time, the first step is to measure a new tool from the manufacturer and to define the minimum permissible length together with the customer.
Then, the TCM tool expert, in cooperation with our grinding specialists, creates exact regrinding instructions that contain all technical data as well as any special requests from the customer.
TCM form of regrinding instructions for step drills:
These regrinding instructions and CNC grinding programs belonging to the respective tool are managed centrally.
Particular attention must be paid to the rounding of the main cutting edges and the coating of the drills. These data are also stored in the regrinding instructions.
If the main cutting corners of a drill have been damaged too much or if there is a complete break, the tool concerned must be cut off at the front and re-sharpened.
After grinding the tip geometry and the stepped cutting edges of the drill, the main cutting edges are rounded.
This is done by means of brush or drag grinders depending on the application of the tool.
The size of the rounding is adapted to the respective drill diameter and the material to be machined.
The main cutting edge rounding (for new tools and regrinded tools) is measured using a 3D measuring microscope from Alicona.
TCM uses optical tool measuring devices of the Heli Check type to measure the drill tip geometry, the step edges and length dimensions.
Finally, the drills are recoated externally at the coater.
If drills are regrinded frequently, the tool must be stripped after a few regrinding cycles in order to be able to guarantee good adhesion of the coating.
In close cooperation with the leading coating companies, the appropriate PVD coatings for the respective application are determined.
It is also important to constantly check the outside diameter of the drill!
The cylindrical bevels of the drill bits are not machined on the outside diameter during regrinding, but are subject to permanent abrasion with every use.
This must be taken into account, especially after regrinding the drill several times.
It is for this reason that the outer diameter in the area of the main cutting corner is checked in advance by our employees during the incoming goods inspection!
Heavily worn round bevel after repeated use of the drill:
In the case of increased round grinding bevel wear on the outside diameter, the following problems usually occur:
• Bore tolerance below target, bore undersized
• Core hole thread too small (tool life of the tap)
• Pilot hole too small for subsequent reamer (tool life of reamer, chips)
• Compaction of the bore wall (lack of taper)
• Bad hole surface (lack of taper)
After grinding, the tools are laser-marked on the shaft for permanent identification.
The number of regrinds is also marked on the shaft.
On request, we can also carry out a wear analysis for the customer on the used tool in order to be able to derive the next optimization steps on site in the project.
After the final inspection and careful packaging of each individual tool in its own protective cover, it is delivered to the customer.
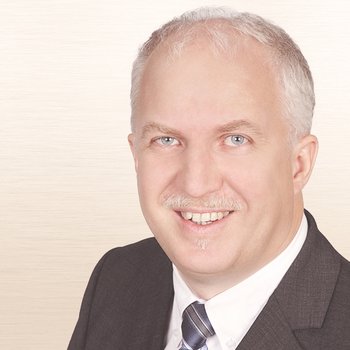
With more than 40 years of broad cutting experience, TCM is an attractive technology partner.
oscheibenbauer@tcm-international.com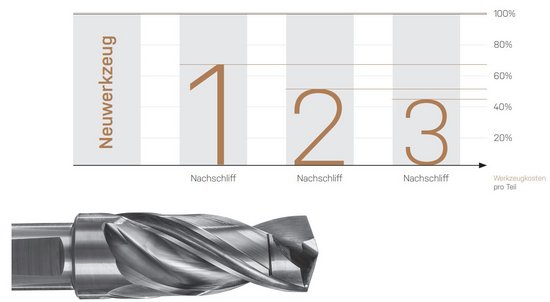