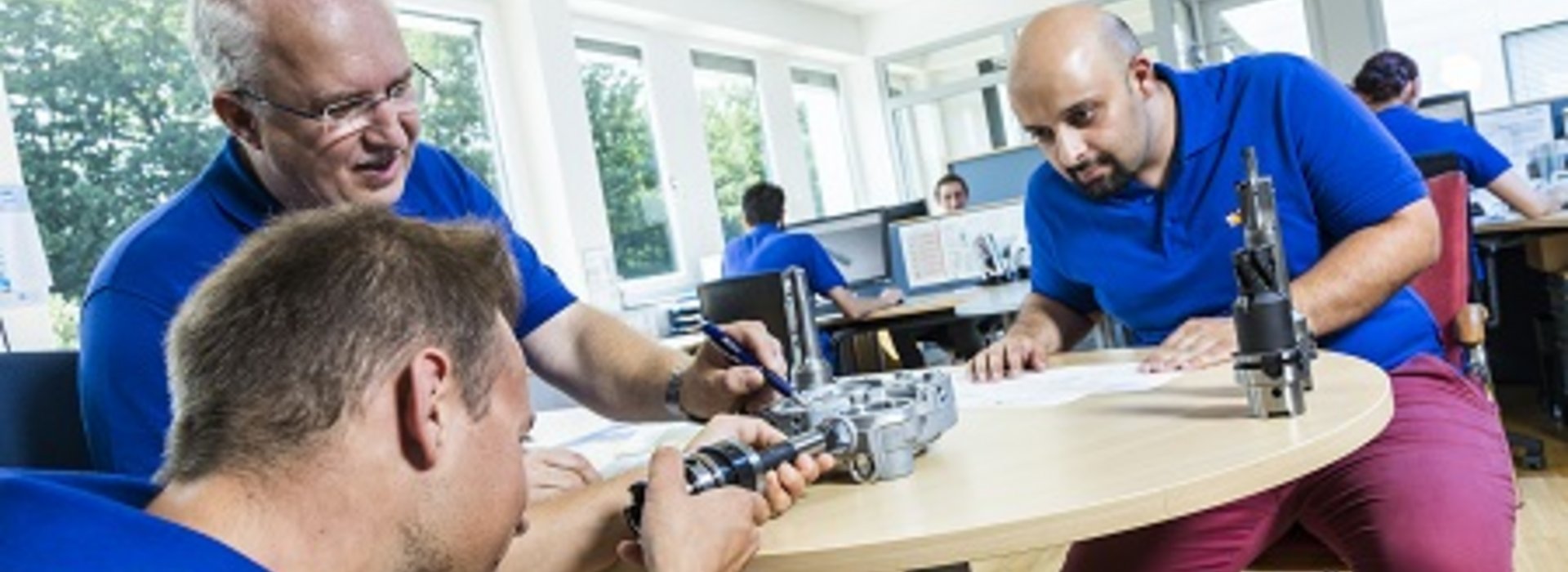
The power is in the cutting edge!- Part 3
Increase productivity through multi-edged precision tools
Special materials require special skill and dexterity in processing. The special tools from TCM convince with precise sensors, as if they were made by a master - and at top speed.
Examples of success
• General face milling & aluminum die castings:
PCD face milling cutters are used today for face milling of die-cast parts in series production. The basic body of these tools is made of aluminum for reasons of weight with screwed-in milling cassettes which are equipped with soldered PCD cutting edges or PCD inserts. Because of the high speeds (cutting speeds of vc 2000 - 3000 m / min !!!) the tools are also finely balanced.
The diameter and height of the milling cassettes can be precisely adjusted to the nearest thousandth of a millimeter. Each PCD cutting edge is applied directly using a high-pressure coolant jet.The decreasing of the PCD milling cartridges, enables to double the number of teeth, by using the same milling diameter. The decreasing of the PCD milling cartridges, enables to double the number of teeth, by using the same milling diameter. The cassettes are shaped so that the chips are guided away from the component! Doubling the number of teeth thus halves the machining time.
• Solid drilling with solid carbide drills:
Until recently, it was state of the art to drill holes in steel materials with double-edged solid carbide drills.
These drills usually have 2 spiraled chamfers on the outside diameter. For larger demands on the hole accuracy and hole surface, there are also solid carbide drills with 4 guide chamfers in the manufacturers' catalogs. The feed / rotation of the solid carbide drill depends on the diameter and is limited by the use of 2 cutting edges.
3-edged drills for drilling gray cast iron and cast aluminum materials have been around for a long time.
With these materials, extremely short chips are created during drilling which can be easily transported out of the borehole.
However, the situation is different for steel materials.
By developing three-edged solid carbide drills for drilling steel materials, there is now new potential for optimization: The use of modern 5-axis CNC grinding machines and new diamond and polishing grinding wheels has led to the development of new tip geometries and newly profiled / polished flutes. This means that the comma-shaped chips generated when drilling steel materials can now be optimally removed even with 3 flutes. Thanks to the 3 flutes, a better bore shape is achieved. The new tapering of the drills also has excellent drilling and centering properties.
The feed / revolutions can be increased by 30% for the same drilling diameter.
The processing time is reduced accordingly!!
• Bore finishing with precision reamers:
Carbide reamers have always been used in series production to finish fitting bores. Depending on the diameter size, these reamers were designed with 4 to 6 or 8 cutting edges. As further development steps, the teeth of the reamers were given an uneven angular pitch. The unequal spacing of the Cermet cutting edges, leads to a better circularity of the reamed bore holes. For steel processing, the carbide cutting edges were also coated with PVD to further increase the tool life.
The latest technology is the use of cermet as a cutting material. Cermet is even more wear-resistant than carbide and hardly forms a built-up edge. In addition, the cutting speed when reaming was doubled compared to carbide reamers.
The development of reamers with a high number of teeth has also made it possible to double the feed / revolutions, which has resulted in extreme time savings, particularly with large bore lengths.
With these high-performance reamers, special attention must be paid to the cooling system.
Depending on whether a blind hole (using a central cooling channel / chip removal to the rear) or a through hole (cooling radially directly to the cutting edges / chip removal to the front) is being machined, the correct reamers must be selected. Since reamers are always finishing tools, the chips must be transported away from the processing point as quickly as possible to prevent the chips from adversely affecting the finished bore surface.
By using such closely divided reamers, the finish machining of a hole in the tolerance range from IT 6 to IT8, with surface values from Ra 0.3 to 0.6 micrometers, can be carried out in just a few seconds. The higher number of cutting edges also results in a better circular shape of the hole.
Cermet blades can be exchanged after the end of the service life, and the reamers can thus be reprocessed.
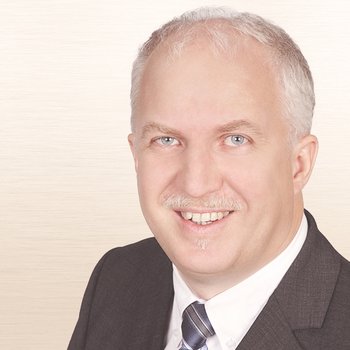
With more than 40 years of broad cutting experience, TCM is an attractive technology partner.
oscheibenbauer@tcm-international.com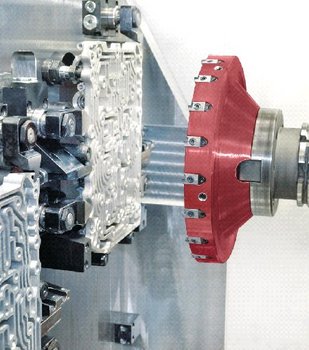
PCD cutter normal tooth pitch
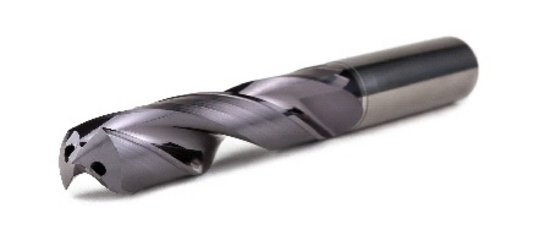
Solid carbide drill with 2 cutting edges
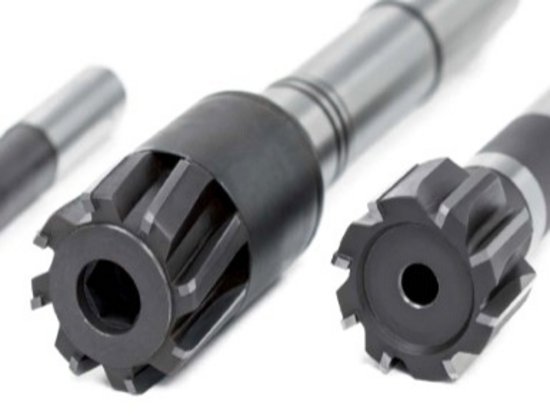
Tungsten carbide / cermet reamer standard
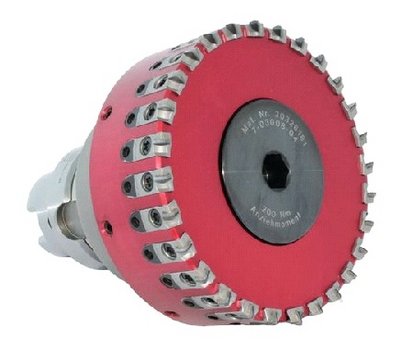
PCD cutter narrow tooth pitch
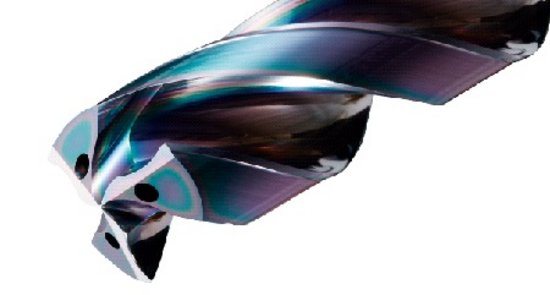
Solid carbide drill, new development with 3 cutting edges
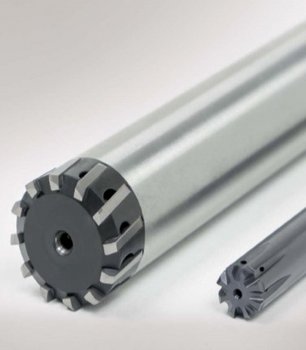