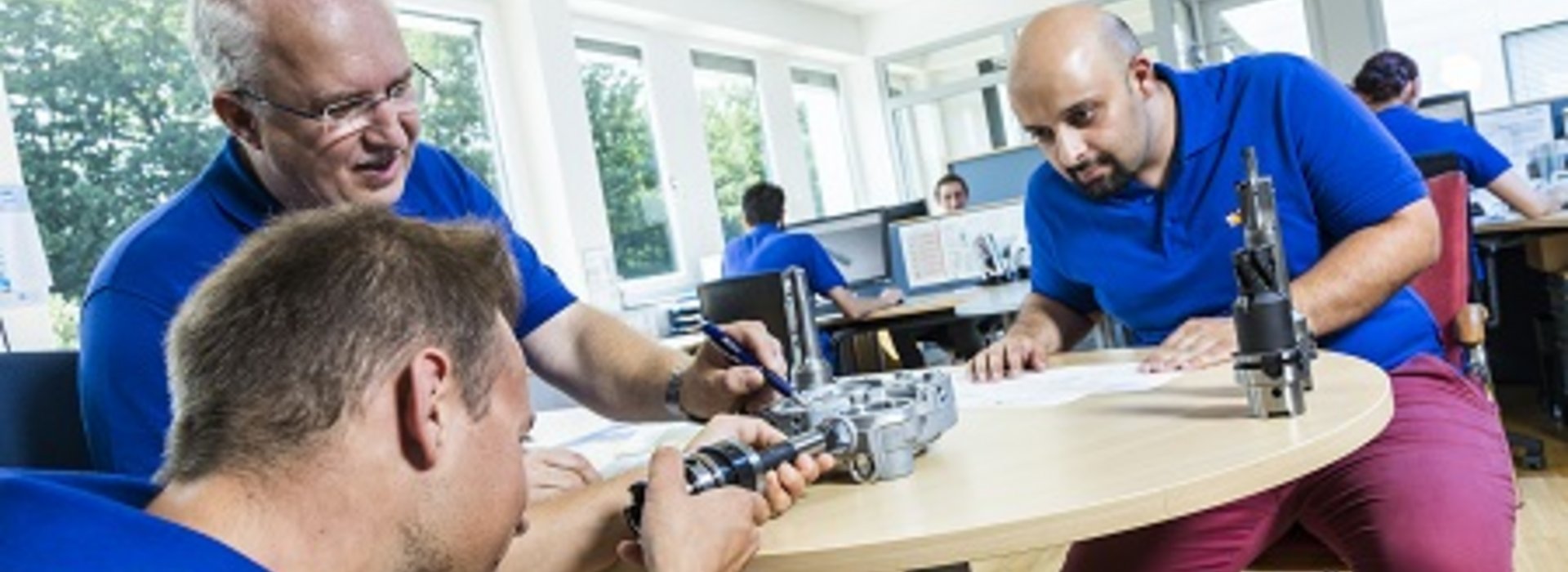
切割中隐藏着魔力!- 第三章
通过多重精密切割刀具提高生产力
特殊材料的加工要求特殊技能和指尖感觉。来自TCM的特殊刀具因其更精确的感应,如同大师亲手制作-以及最高的速度而让人信服。
成功案例
- 平面铣切和铝合金压铸件概述
PKD平面铣刀被应用在当今压铸件的铣切批量生产中。出于重量的原因这个刀具的主体部分由铝合金组成,上面布满用螺丝固定的铣刀带,铣刀带由多个焊上的PKD割刀或PKD转移板组成。由于高转速(线速度达2000-3000米/秒的切割速度!!!)刀具也被轻微抬高。
铣刀带能够被在直径上以千分之一毫米的范围调整,每个PKD切割都直接通过高压冷却介质来降温。铣刀带的排列形状使得切割碎屑很容易被排除!双倍的齿数带来了加工时间的减半。
- 用高硬度金属钻头的全钻孔
用双切割高硬度金属钻头在金属原料上钻孔,不久之前还是技术的前沿。
这些钻头通常在外直径上有两个螺旋形引导棱角。当钻孔精度和钻孔表面有更高的要求时,制造商的产品清单里也会提供那种带4个引导棱角的VHM钻头。VHM钻头的走刀和旋转是跟直径相关的,并且只能在两次切割的场景中应用。
3次切割的钻头已经在灰口铸铁和铝铸原料的钻孔上应用很久了。然而在这种原料上钻孔会产生极其细小的碎屑,并且很难从孔洞内排除出去。
通过研发金属原料钻孔三次切割的VHM 钻头,现在有了新的优化潜力:先进的5轴CNC修磨机床和新型的金刚钻及抛光磨片被投入使用,带来了新型的尖端几何和新的轮廓清楚的碎屑槽口的发展。通过这些,那些在金属原料钻孔时产生的细小碎屑现在也可以通过3道碎屑槽口最佳地疏导出去。通过这些3道碎屑槽口还能达到一个更好的钻型。新型的钻头尖端同时还具有出色的起钻-集中性质。
在相同的钻头直径下,走刀/旋转能被提高30%,同时相应地降低加工时间t!
- 用精细绞刀进行的钻孔精加工
在通孔钻的最终加工上,高硬绞刀一直在批量生产中得到应用。随着直径大小的变动,从4到6亦或8道切割的绞刀都会被用到。作为更进一步的发展步骤,带不同棱角间距绞刀齿也被装备上,由此使得孔圆更完善。在金属加工时,一般为提高加工寿命都会给硬金属切割进行PVD涂层。
当前最新的科技水平是用使用合金陶瓷做切割材料。合金陶瓷比硬质金属更耐磨,不会形成切削流,另外切割速度也能比硬金属铰刀快一倍。
通过研发具备更多齿数的铰刀也能使走刀和旋转次数翻倍,对深孔钻来说特别节省时间。
使用这些高效率的铰刀时首先需特别留意冷却系统。
如何挑选正确的铰刀,取决于是加工未通孔(使用一个中心冷却通道/碎屑向后排)还是贯通孔(冷却液直接放射状射向切割点/碎屑向前排)。鉴于铰刀在生产过程中被连续使用着,碎屑必须尽可能快地从加工点被排除出去,这样才能防止碎屑损伤到已经完成的钻孔表面。
通过使用这样紧密分配的铰刀,可以使钻孔的加工在几秒钟内完成,并保持容差在IT6至IT8之间,以及表面值在Ra 0.3到0.6微米的范围,在加工更多切割部件的同时还保证了更好的钻孔圆形。合金陶瓷铰刀可以在使用期结束时更换,以便铰刀得到修磨保养。
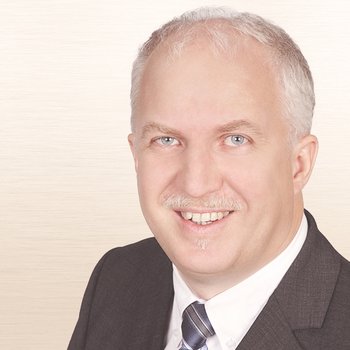
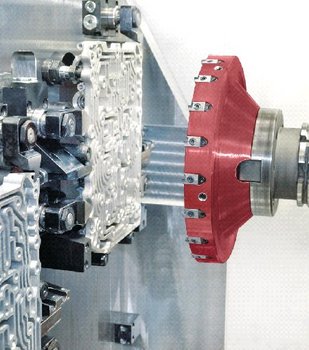
PKD铣刀直径100毫米普通齿间距
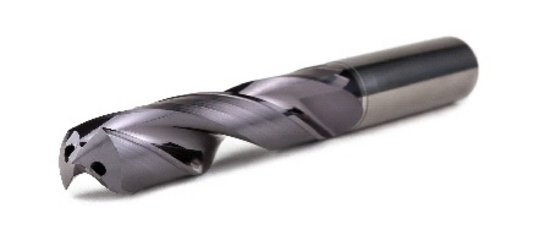
VHM两刀钻头
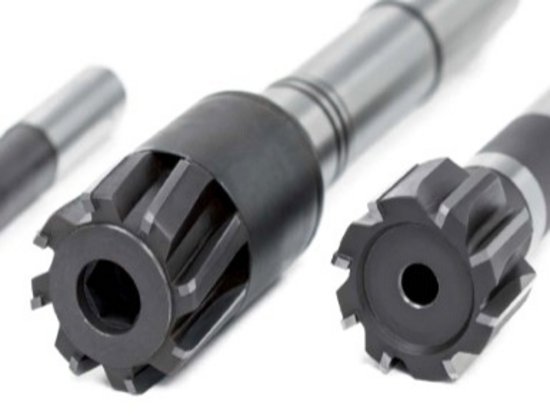
标准硬金属/合金陶瓷铰刀
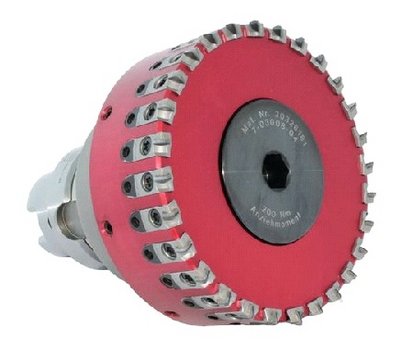
PKD铣刀直径100毫米紧密齿间距
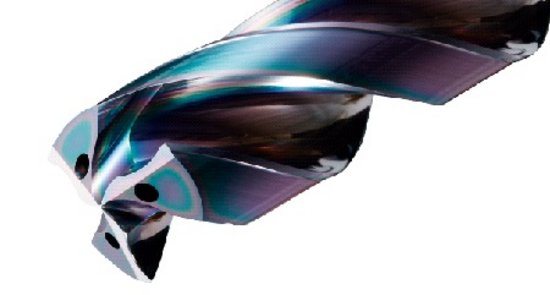
VHM新开发的三刀钻头
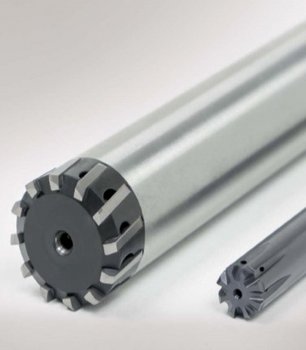