![[Translate to English:] [Translate to English:]](/fileadmin/_processed_/2/1/csm_CreatorKit-Laufrad-V1_29e4cdf058.jpg)
Turning of rubberized track rollers with diamond turning tools
Since April 2022, TCM Austria has been working on a Level 3 tool management project for a well-known Austrian manufacturer of safety-related elevator components. At this site, safety components, door mechanisms and car frames are produced with high quality requirements. Part of this production includes the machining of different dimensions of travel wheels, which are used to safely guide the elevator in the car frame.
The impellers consist of a cast aluminum base body on which the actual running surface is rubberized. The center bore, flat surfaces and rubberized tread must be turned on the CNC lathe in a single setup to ensure optimum concentricity during operation. Turning the aluminum surfaces is straightforward, but turning the rubber treads of the track rollers with conventional turning tools was not possible due to the soft condition of the rubber surface. Even using high positive, sharp carbide cutting edges and polished rake faces, a satisfactory result could not be achieved. In order to solve the machining problem, TCM was called in due to the high savings potential within the scope of tool optimization.
TCM's team of toole experts developed a new tool concept that included the use of polycrystalline diamond (PCD) as the cutting material. The cutting edges were laser machined for highest cutting edge sharpness and equipped with an extreme rake and clearance angle for highest cutting ability and lowest chip pressure. The turning holder was designed as a monoblock for maximum stability, and the polished surface of the PCD cutting segment prevents chip sticking. In addition, a small corner radius was added to protect the sharp cutting corner. After the tool was designed, it was manufactured in our cutting laboratory. The PCD cutting edges were brazed and laser cut at TCM partner DIBO Diamond Tools.
After the tools arrived, the first turning tests were carried out on a cycle-controlled lathe and then transferred to the production CNC lathe.
Thanks to the innovative tool concept and adapted cutting values, naturally hard rubber can be machined effortlessly without the need for costly freezing of the rolls. This is possible because the lasered PCD cutting edges cause neither compression nor burning of the rubber due to their sharpness and polished rake face. In addition, there are no unwanted vibrations or shading on the machined running surface during soft cutting. Since rubber does not produce chip breakage, only a thin continuous band is produced during turning, which is discharged through the specially shaped chip chambers of the special turning holder.
In the TCM machining laboratory, a surface inspection was also carried out using the Alicona measuring microscope. Here, the turning depths, which are precisely reproduced in the rubber, were made visible by a 3D measurement of the surface structure. By varying the tip radius on the PCD cutting edge and adjusting the feed rate during turning, the surfaces desired by the customer can now be produced in a targeted manner.
The PCD cutting edges of the turning tools can be easily exchanged and reconditioned several times at DIBO Diamantwerkzeuge GmbH.
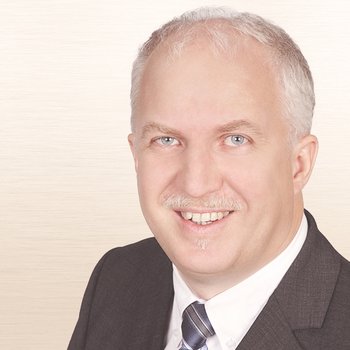
With more than 40 years of broad cutting experience, TCM is an attractive technology partner.
oscheibenbauer@tcm-international.com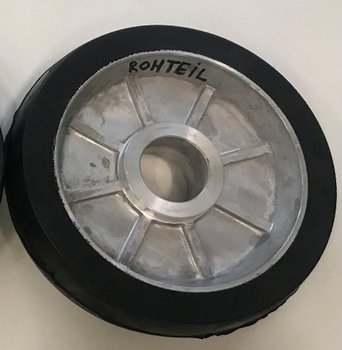
Impeller blank
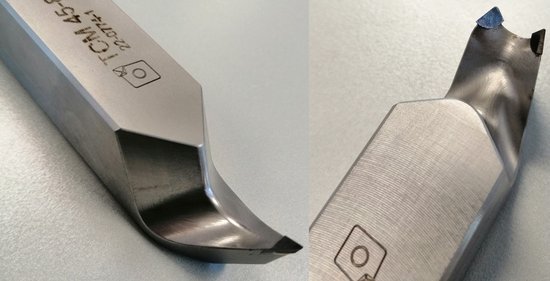
TCM PCD rotary holder
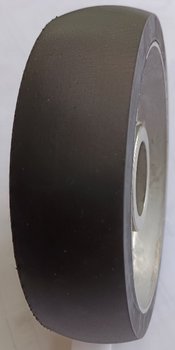