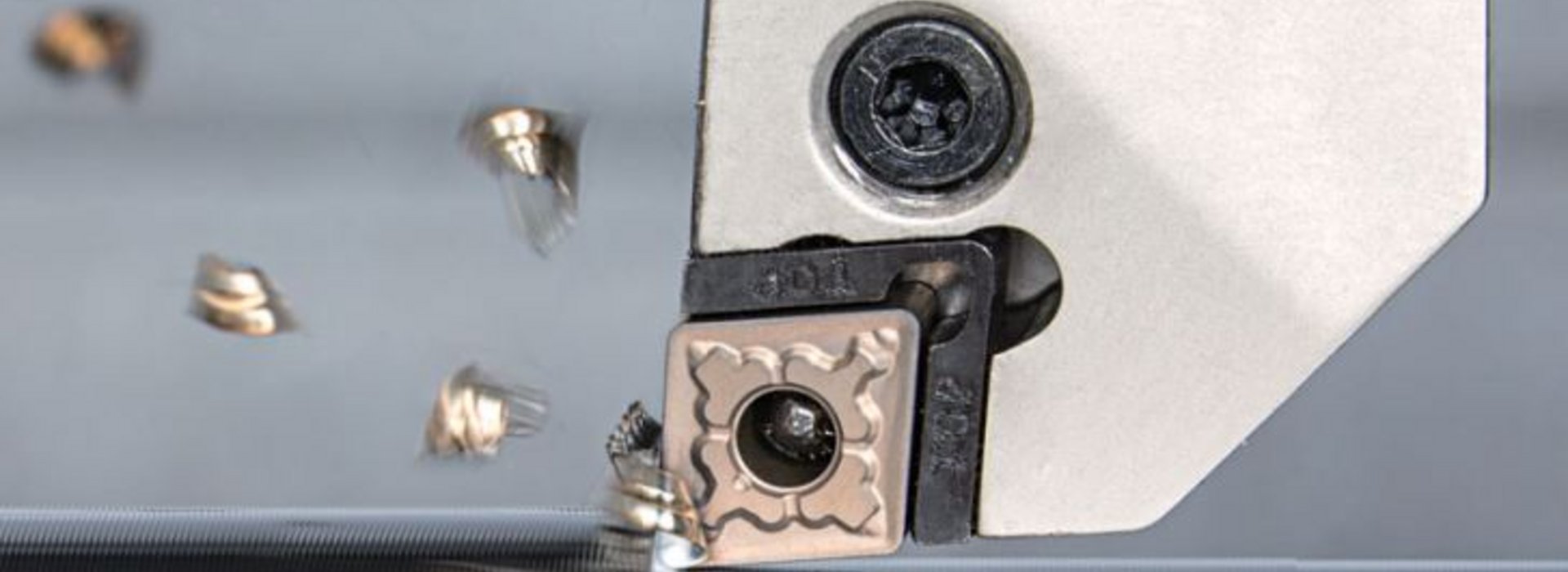
Reduction of tool costs - when turning with ISO inserts
Significant reduction of tool costs and expanded possibilities in turning thanks to new insert shapes.
Despite modern turning processes such as high-feed turning and innovative turning concepts that allow turning in both feed directions, more than 80% of all turning operations, with the ISO inserts that have been in use for decades, are still performed in the familiar sizes.
Continuous improvements were made to the carbide qualities, coatings and chip grooves. Due to these technical improvements, in combination with better purchase prices at higher consumption quantities, a certain reduction of tool costs could also be realized. Market research conducted by insert manufacturers shows that in most turning processes, the maximum depths of cut possible for the existing ISO insert sizes are rarely achieved!
Worldwide, 75 % of all turning operations are still carried out with a maximum depth of cut of 3 mm! The standard ISO inserts are simply too large, especially for the finishing area, where machining is usually performed with a depth of cut of only a few tenths of a millimeter.
Since this also makes no sense from an ecological point of view, smaller inserts have been developed in the meantime, which allow a much more efficient use of the expensive cutting materials. Although smaller inserts were already manufactured a few years ago, these inserts were normally only scaled smaller. This made the chip grooves and insert height smaller, leading to chip jams and cutting edge breakage when machined with the same working parameters. The downsized inserts could in no way achieve the performance of the full-size inserts and thus could hardly establish themselves in the market.
To be successful here, the inserts must retain both the height and the original size of the chip grooves. With the new, smaller ECO size inserts, equivalent results can now be achieved, up to a cutting depth of 3 mm. Furthermore, tooling costs are reduced by 25-30% depending on the insert shape.
Topic rotary holder ECO sizes
Normally, for clamping the smaller inserts, both for external and internal turning, turning holders with smaller insert seats are needed, which are now available from manufacturers. However, this requires additional investment.
To circumvent this, special cassettes have been developed for the insert mold.
The enclosed cassettes are positioned in the insert seat. Small magnets hold the cassettes in position so that no problems can arise during insert changes in the machine. As a result, all existing turning holders in the plant with standard ISO insert sizes, can be converted to the smaller ECO turning inserts more easily and at lower cost. The f dimension (cutting tip to holder unit dimension) also remains the same as a result.
In addition, to smaller and more economical inserts, inserts with smaller tip angles have been developed:
YNMG insert
With a very slim point angle of only 25°, the YNMG insert offers better usability for copy turning and better accessibility for back turning and turning corner undercuts. At the same time, 4 cutting edges can be used in the double-sided version (YNMG). This insert can be clamped in the standard turning holder for the VNMG insert (point angle35°).
GNMG and FNMG insert
The point angle of the two inserts, GNMG and FNMG, was also reduced. For the GNMG, the point angle has been reduced to 45° (ISO DNMG 55°) and for the FNMG, the point angle has been reduced to 70° (ISO CNMG 80°). In addition, both inserts can be used on both sides and are therefore 4-bladed.
The smaller point angle results in the following advantages compared with the previous
ISO inserts:
- Better accessibility to the workpiece
- Improved chip evacuation when turning faces and shoulders
- Better chip control
- No scratching of the workpiece surface by chips
- Lower radial cutting forces
- Less vibration
The GNMG and FNMG inserts have the reduced point angle sintered only in the front cutting area. The remaining areas of the insert have the same basic shape as the ECO CNMG09 and ECO DNMG1104 inserts. Here, too, it is possible to use the existing ECO turning holders or ISO turning holders with cassette.
Do you want to significantly reduce your tool costs during turning?
Do you need more trouble-free turning processes?
Do you want to increase productivity?
We are always available for trials in your production!
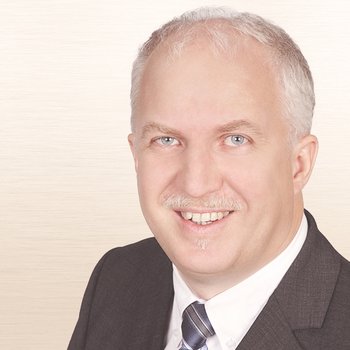
With more than 40 years of broad cutting experience, TCM is an attractive technology partner.
oscheibenbauer@tcm-international.com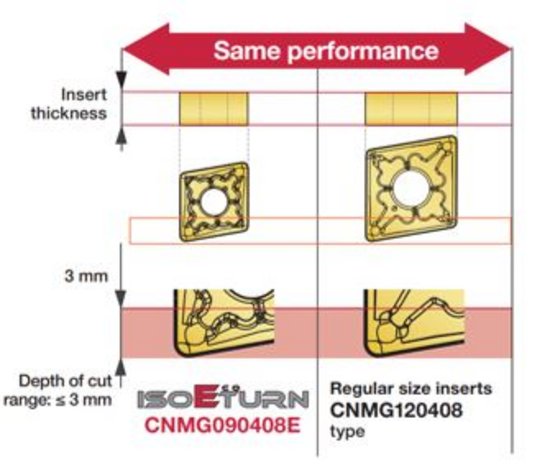
Size comparison of ECO insert size 09 with ISO standard size 12, using the example of the rhombic insert.
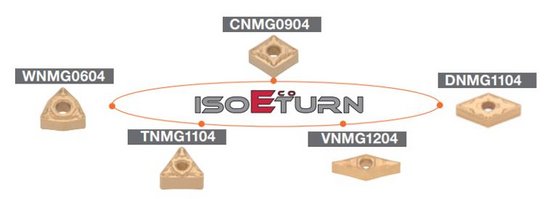
Available ECO insert sizes and shapes with chip grooves for finishing, medium and roughing applications in carbide and cermet cutting materials.
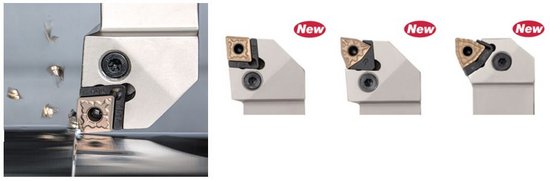
Mounted shims - cassettes in rotary holder
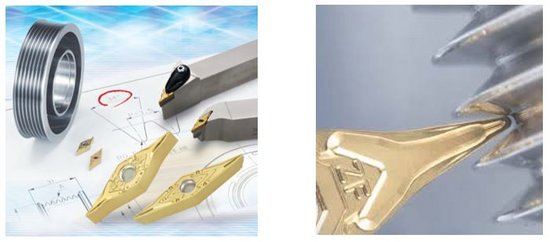
YNMG insert Possible applications
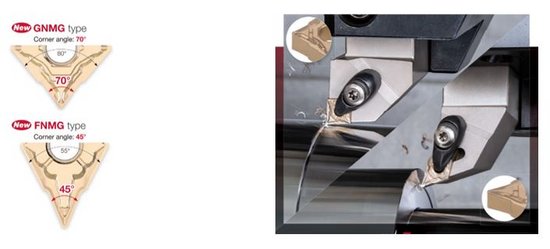
Tip angle GNMG and FNMG / GNMG and FNMG clamped in ISO clamping holder
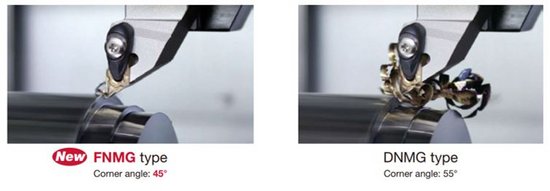