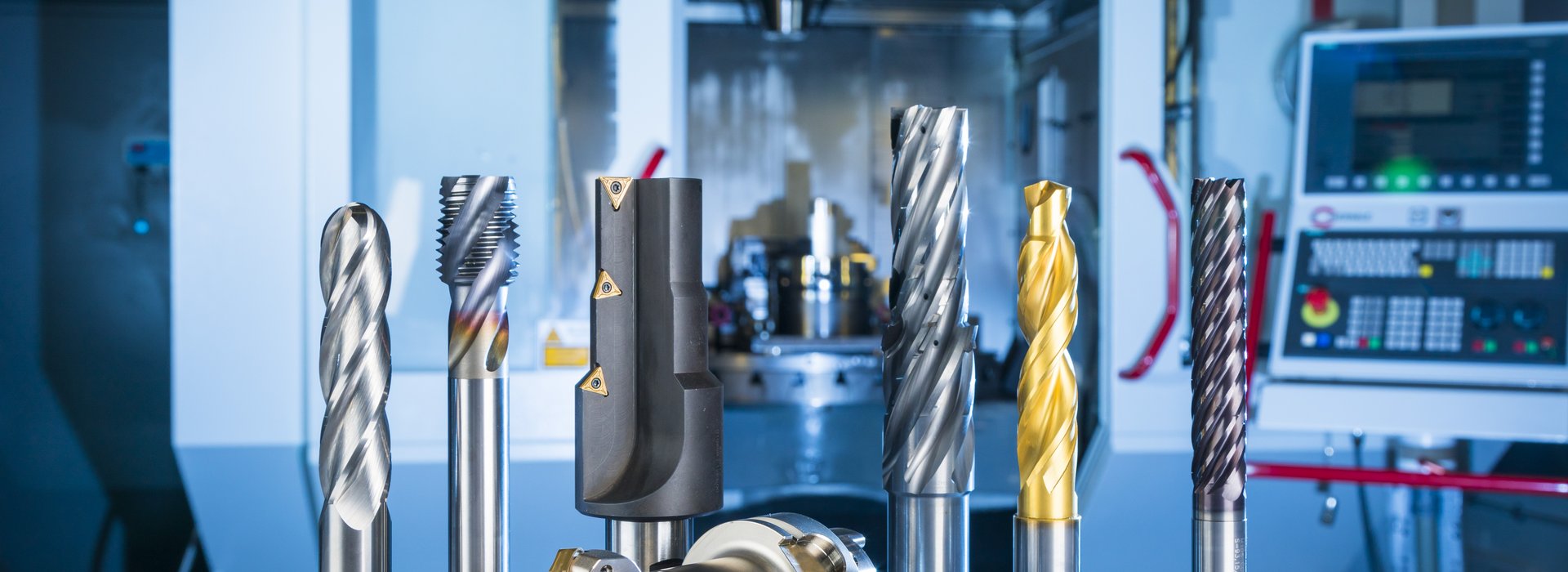
Re – Tooling with the TCM Team of Experts:
The TCM tool experts are not only busy with the creation of complete tool layouts for the production of new parts.
It is often also a customer request, which is absolutely necessary from a cost perspective, to completely rework components that have been produced in-house for a long period of time, both in terms of tool technology and the machining strategy.
An intelligent design of the cutting tools in conjunction with advanced machining strategies and the optimal use of the machine dynamics and programming options available on-site, lead to a significant reduction in machining time.
Re - tooling at TCM is therefore an often used, efficient method for optimizing serial parts.
Key points in the TCM Re-tooling process:
1) Technical analysis at the customer's site Technische Analyse beim Kunden Vorort:
- Live recording of the current machining sequence on the machine
- List of currently used tools
- Determining the processing time per machining step
- Determination of the total processing time of the part
- Evaluation and analysis of the data
- Determination of the tool costs / component (CPU) if necessary
- Checking the current part tensioning
- The optimization goal is discussed and agreed together with the customers
2) Redesign of tools and machining strategy
- Selection of modern standard tools from the entire market
- Planning and construction of special tools
- Optimization of the cutting values
- Use of modern machining strategies (drilling thread milling, trochoidal milling)
- Checking the clamping device (multiple clamping possible? Accessibility?)
- Creation of a TCM processing proposal
- Comparison of the production times, old and new
- Calculation of the savings
- Quotation to the customer
3) Implementation after the customer survey Implementation after the customer survey
- Production and ordering of the tools
- Support with CNC programming
- Provision of all 3D tool data
- Provision of all digital tool data sheets
- Breaking-in of the tools together at the customer
- Documentation of results and customer acceptance
Practical example:
Fertigung Hydraulikblock 300x300x200 mm
Material S355J2+N
BAZ Horizontalbearbeitung
Customer request : Reduction in processing time – 25 %
Practical implementation with TCM:
- 3 days, as-is analysis on site, collection of all data
- Use of modern spiraled solid carbide deep hole drills
- Use of new inserts for better chip breakage when drilling
- Change in drilling strategy and drilling sequence
- Optimization of cutting values for drilling, milling, and threading
- Use of special step drills
- Tapping with internal cooling and synchro lining
- Avoidance of empty paths in the CNC program
- Regrouping the tools in the machine tool magazine
- Perfect regrinding service
Result : Reliable reduction in processing time -32 %
Avoidance of long chips when drilling and threading
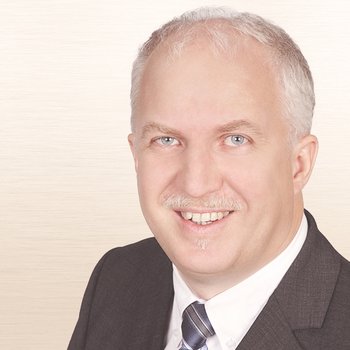
With more than 40 years of broad cutting experience, TCM is an attractive technology partner.
oscheibenbauer@tcm-international.com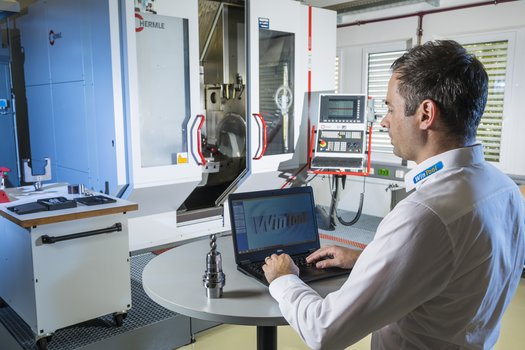
Analysis of the current status at the customer
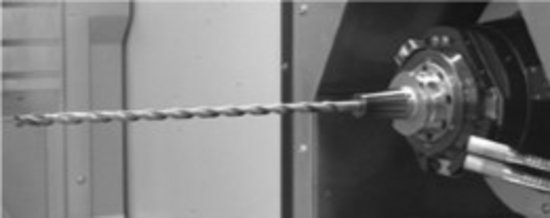
Spiraled deep hole drill solid carbide 30xD
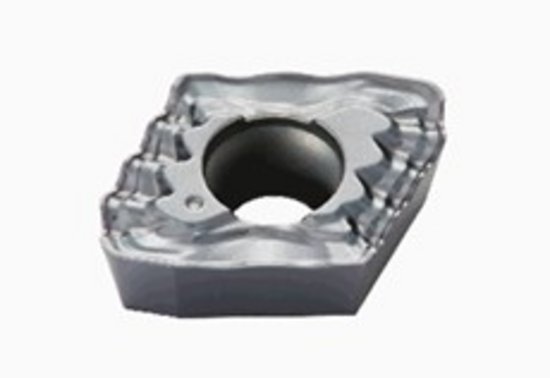
Drill bit with optimized chip breaking geometry
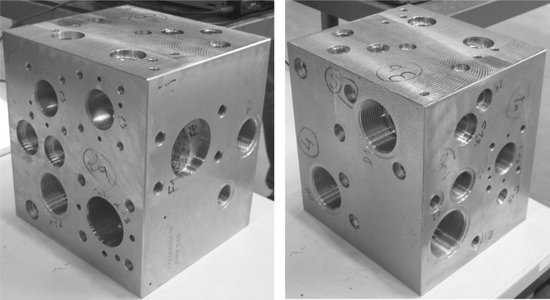