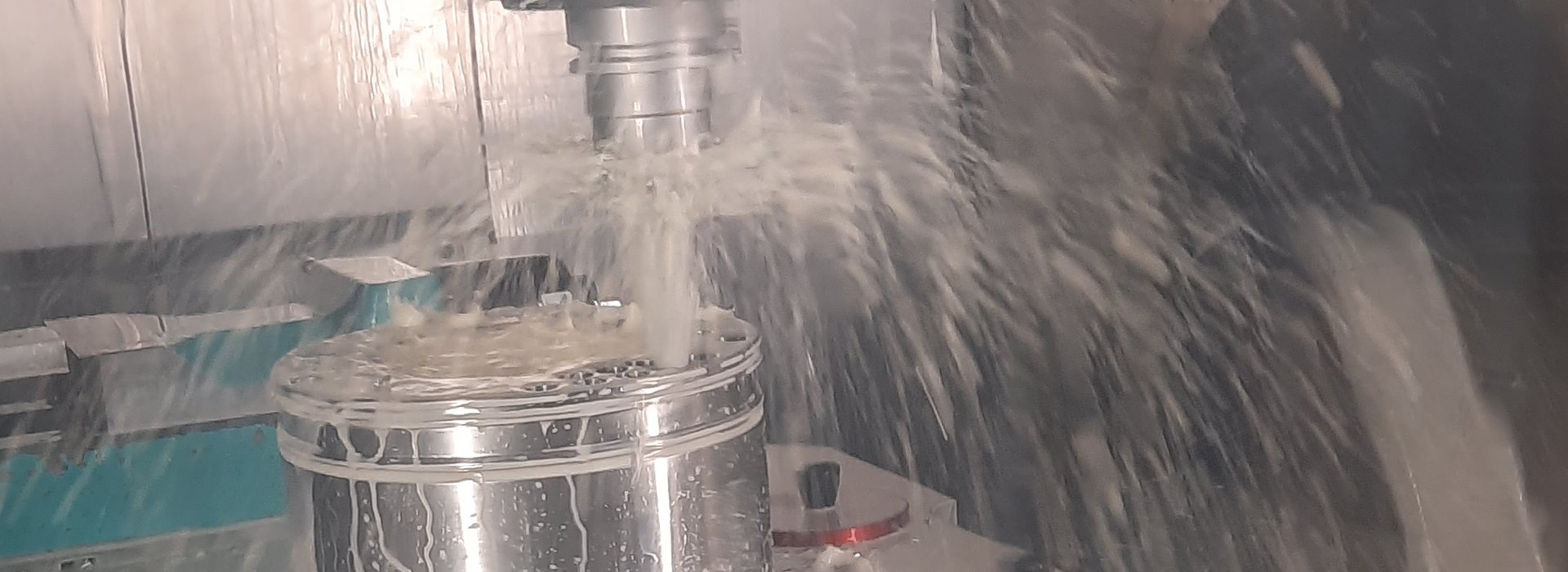
Optimization of deep hole drilling in the AEC machining laboratory
One of the main purposes of the AEC (Application Engineering Center) has always been to be able to optimize difficult machining processes in a laboratory environment without disrupting the customer's production. Once the desired result is achieved after several optimization steps, this technology can then be easily duplicated on the customer's machine. Our machining center and peripherals have been designed to replicate as closely as possible the actual production conditions of each TCM customer. High-pressure cooling, compressed air through the spindle, and minimum quantity lubrication (MQL) are all available, as are all variants of modern tool holding fixtures and programming systems, in order to be able to apply modern machining strategies.
Main tasks of the AEC machining laboratory:
- Tool tests (service life, function tests, surface on the component)
- Machining of new materials of the customers
(machining strategy, cutting value optimization)
- Cutting force, torque and power measurement (Kistler and Toolscope)
- Tool measurement (Zoller Smile)
- Exact inspection of tool cutting edges and wear (Alicona)
- Execution of tool training courses (TCM Academy)
- Customer seminars with TCM tool suppliers
Current practical example / process optimization deep hole drilling:
Customer component:
Steel cylinder, material stainless steel, 1,200 N/mm², forged
12 holes
Diameter 13,5 mm
Drilling depth 135 mm (10 x D)
Customer tool:
Deep hole drill with carbide interchangeable tip diameter 13.5 mm
Steel body, spiralized , max. drilling depth 12xD
Internal cooling
Pilot holes depth 2 x D.
Issue:
In the diameter range below 16 mm and for drilling depths above 8 x D, the steel bodies used have considerably less torsional and bending stiffness, than a solid carbide drill.
Due to the large cutting forces during full drilling of this tough-hard material, strong vibrations occur during drilling, which have a negative effect on the tool life of the indesable drill heads.
The additional interface between the drill head and the steel body is also rather disadvantageous.
In the customer trials, it was possible to drill, but there was a permanent drilling process and, as a result, cutting edge and base body unstable beakes. Significant vibration noises could also be heard, especially in the lower area of the holes where chip removal naturally becomes more difficult.
The only sensible alternative, a spiralized solid carbide deep hole drill, could not be organized for further tests, since all tool manufacturers do not have solid carbide deep hole drills with a diameter of 13.5 mm and a drilling depth of 10xD in their catalog range.
TCM improvement:
TCM partner, the company OSG has developed a new type of for drilling stainless steels.
This geometry, called ADO - SUS, has the following advantages:
- Enlarged cooling channels (better cooling due to higher flow volume)
- Smaller margins and larger back taper (less friction)
- Sharper cutting edges (less cutting forces)
- New profile shape of the flutes
- Optimized, smooth coating (low built-up edge formation)
TCM decided to have these drills manufactured by OSG, as a special tool for the planned tests, in order to be able to use the best drilling tool for this application.
Experimental results:
Optimized cutting values : Pilot hole vc = 60 m/ min Feed rate fu = 0.30 mm/ U
Deep hole drilling vc = 50 m/ min Feed rate fu = 0.32 mm/ U
Straightness of the holes greatly improved
Constant torque curve over the entire drilling length
Low drilling noise
Optimum of chips shape
Chip removal from borehole unproblematic
Coolant pressure 45 bar
Emulsion 8%
Hydraulic chuck HSK63-A / diameter 14
The ADO - SUS drills can also be regrinded several times
In several test series the following result could be achieved by the close cooperation of TCM and OSG Toolexperts:
Drilling time / customer: 40.5 sec
Drilling time / TCM: 17,5 Sec
Customer footprint: 8 m Drilling path 6 components
Footprint TCM : 23 m drilling lenght 17 components
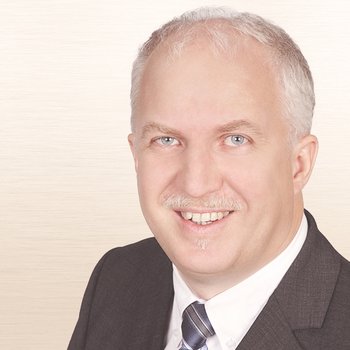
With more than 40 years of broad cutting experience, TCM is an attractive technology partner.
oscheibenbauer@tcm-international.com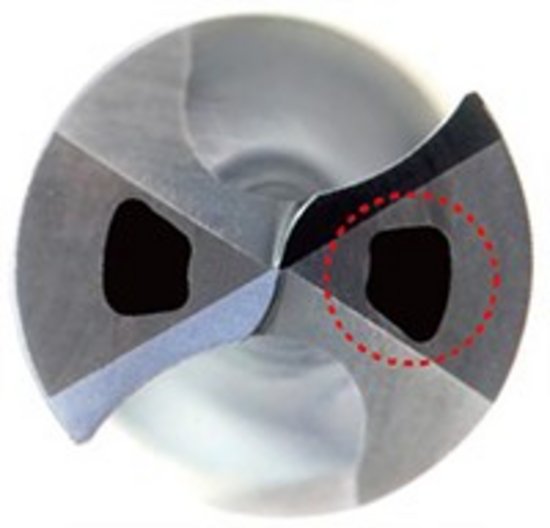
Enlarged cooling channels
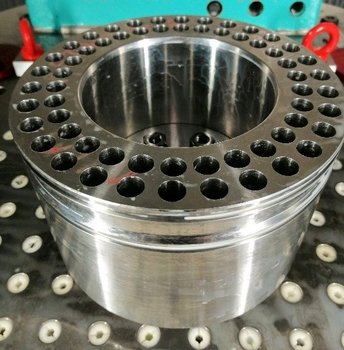
Experimental arrangement drilling
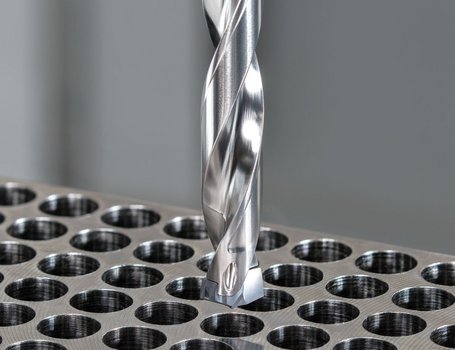
Deep hole drill 8xD with interchangeable head
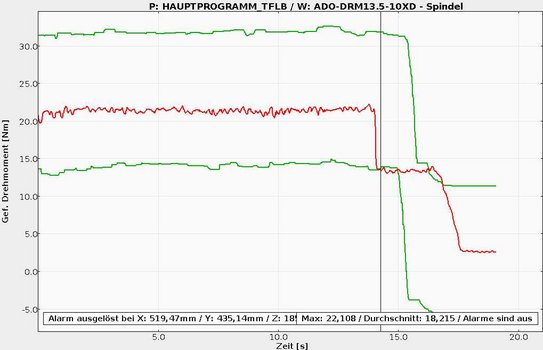